Leading steel manufacturer Salzgitter Flachstahl showcased their new low carbon steel manufacturing process using our visualisation technology at Hannover Messe.
Showcasing SALCOS® through visualisation
With such a far-reaching project in progress, it’s no surprise that the team at Salzgitter wanted to use the Hannover Messe exhibition to showcase SALCOS® so we were delighted when they turned to us to create an inspirational visualisation solution.
Our solution gave visitors the chance to see for themselves the new production process without leaving the comfort of the Salzgitter Flachstahl exhibition stand.
Our highly accurate scale data meant that delegates were able to experience new electrolysis systems for producing hydrogen, a direct reduction plant more than 100 meters high as well as an electric arc furnace. This made Salzgitter Group the first company to present a real works topography using actual construction data as virtual reality.
The project was highly complex, involving the import of extensive sets of data in multiple formats to create an accurate and detailed output from Visionary Render, our immersive software platform.
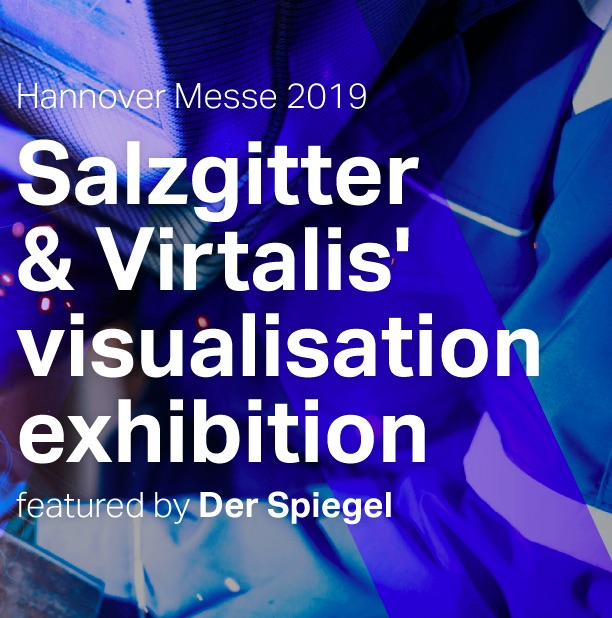
Visualisation technology leads to stronger engagement
Our project for Salzgitter Flachstahl clearly demonstrates the benefits of using visualisation technology to communicate ideas in a clear and engaging way, removing complexity and enhancing understanding.
Visionary Render makes it possible to take data from a number of sources to build a multi-dimensional image of industrial plant and processes which would otherwise be difficult to fully articulate, particularly in an environment like an exhibition, event or trade show where time is limited and the audience is diverse. The fact that we can create scaled structures of plant and overlay with textures, real-life light and shade and features of the built environment and animations, make this an immensely powerful and communication tool, and one with longer-lasting impact on participants.
Key Figures

"Visualisation technology pays dividends when applied to the transformation of production processes because it allows ideas to be shared and tested in a non-live environment"
Hannover Messe brings together some of the world’s largest companies in the engineering sector to share knowledge, ideas and innovation. It’s a key platform for showcasing capability and attracts a significant audience – this year’s event, held in April, was attended by 200,000 delegates from across the globe.
This year Salzgitter Flachstahl wanted to use the exhibition to draw attention to their new low carbon footprint steel-making process, so we were approached to create a highly accurate and engaging visualisation solution.
It was the first time that VR technology was to be used to present real works topography using actual construction data. This was a remarkable success and led to an unparalleled response from delegates and the media. There was significant interest on the company’s exhibition stand, helping Salzgitter cement relationships with customers, partners and stakeholders. The initiative led to wider profile-raising of the company and its drive improve sustainability with an in-depth feature in Der Spiegel, a leading German news publication.
Sonke Dierking, a Senior Systems Engineer with Virtalis, installed a fully fixed, 2 wall and floor CAVE system at Salzgitter. The example was shown at Hannover Messe. This is fully tracked, using Advanced Realtime Tracking (ART). Passing attendees were given a glimpse of what was being shown on the CAVE on an external screen which showed a live feed from inside.
The demonstration was created using Virtalis’ Visionary Render software. Data provided by Salzgitter in the form of CAD and laser scan point clouds was imported and turned into an interactive scene, which told the story of Salzgitter’s hopes for the new site.
About Salzgitter Group
Salzgitter Group is a leading pan-European steel and technology group. Our client, Salzgitter Flachstahl, is the largest steel subsidiary of the Group and in 2017 produced around 4.6m tons of steel with a turnover of €2.9bn. The company is highly innovative, relying on the use of state-of-the-art technologies for steel production and processing, and is now one of the world’s most efficient producers of steel.